Master successful industrial steel fabrication projects with these top 10 tips: meticulous material selection, precise design tolerances, ideal stock gauge choices, uniform bending techniques, strategic cost-effective strategies, and attention to bend reliefs and clearances for structural integrity. Employing advanced technology, quality enhancements, and adherence to industry guidelines guarantee high-quality results. Focusing on these key areas can elevate the success of your steel fabrication projects.
Key Takeaways
- Choose materials wisely for durability and aesthetics.
- Maintain tight design tolerances for precise results.
- Opt for cost-effective stock gauges in fabrication.
- Ensure uniform bends and proper bend radii.
- Pay attention to clearances for structural integrity.
Material Selection
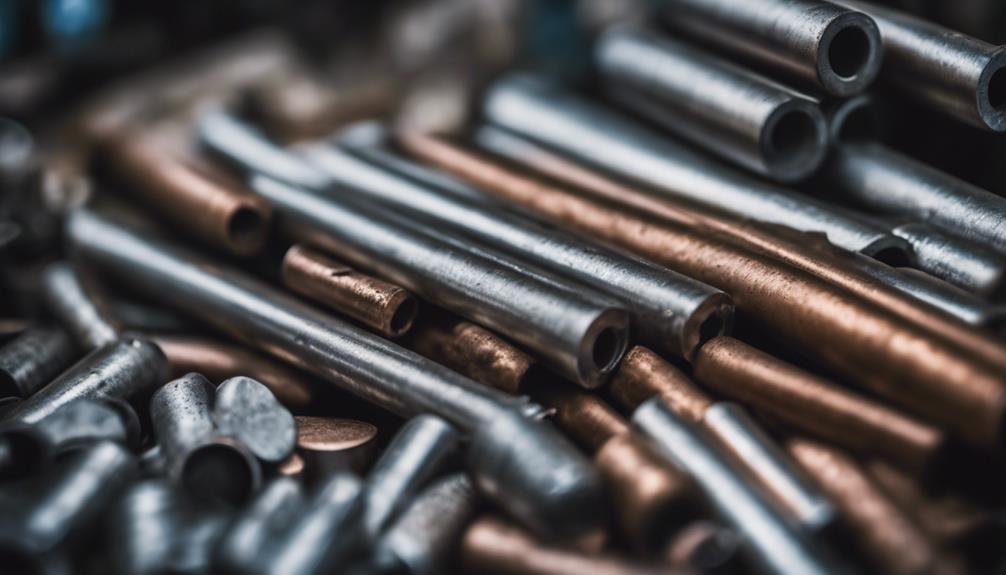
Selecting the appropriate materials plays a crucial role in ensuring the longevity and performance of industrial steel fabrication projects. When it comes to material selection, the choice between stainless steel fabrication and marine-grade aluminum can have a substantial impact on the durability of the final product. For projects that are exposed to harsh outdoor elements, such as marine environments or extreme weather conditions, opting for marine-grade aluminum or stainless steel is highly recommended. These materials offer exceptional resistance to corrosion and rust, ensuring that the structure maintains its integrity over time.
In contrast, materials like copper, zinc, and brass are better suited for indoor decorative projects where they can add aesthetic value without being exposed to the same level of environmental stress. By carefully considering the specific requirements of a project and choosing materials accordingly, industrial steel fabrication projects can not only achieve longevity but also maintain their visual appeal and structural robustness. Proper material selection is a fundamental step in ensuring the success of any metal fabrication endeavor.
Design Tolerances
Understanding design tolerances is paramount in the field of steel fabrication, as they dictate the permissible variations in specified dimensions on blueprints. Design tolerances in steel fabrication refer to the allowable variations in dimensions specified on a blueprint. These tolerances play a vital role in determining the quality and functionality of the final product.
Tight tolerances increase the complexity and cost of fabrication processes but are necessary for achieving precise and accurate outcomes. Deviations from design tolerances can lead to structural integrity issues or functional problems, highlighting the importance of adherence to these specifications. Proper communication of design tolerances between designers and fabricators is essential for project success.
When searching for steel fabrication companies near me, it is crucial to inquire about their approach to design tolerances to make sure that your project requirements will be met accurately. Adhering to design tolerances is key to the successful completion of steel fabrication projects and the delivery of high-quality products.
Stock Gauges
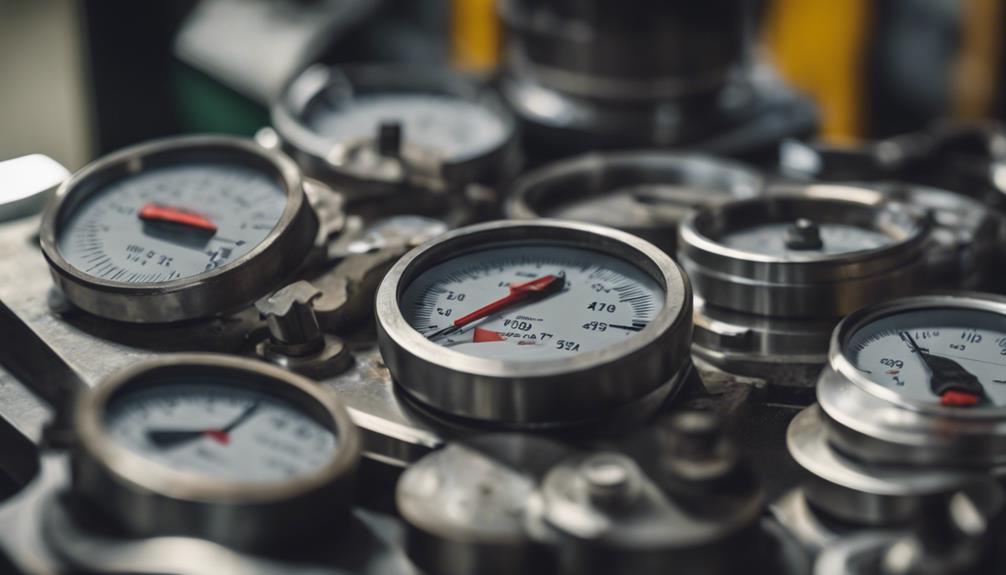
Choosing appropriate stock gauges is a pivotal decision in sheet metal fabrication projects, impacting both cost-efficiency and design feasibility. Stock gauges, which refer to standard thickness options available for sheet metal fabrication, play a pivotal role in the success of a project.
Thicker metals come with limitations on achievable bend angles and may increase costs due to material expenses and processing requirements. On the other hand, thinner and more pliable metals are preferred for intricate fabrications to avoid issues like cracking during the fabrication process.
Selecting stock gauges wisely can lead to more cost-effective and efficient fabrication processes, benefiting both the steel fabrication company and the ultimate end-users, especially in industries like construction where precise and complex metal components are often required.
Standard stock gauges not only help in simplifying designs but also contribute to reducing overall project expenses, making them a key consideration in steel fab for construction projects.
Uniform Bends
To guarantee maximum efficiency and cost-effectiveness in industrial steel fabrication projects, maintaining uniform bends on the same plane is vital for streamlining the bending process. Machines have limitations in bending objects in different directions without reorienting, making it imperative to confirm all bends on the same plane bend in the same direction.
Keeping bends in the same radius not only saves money by reducing the need for extra steps in bending and reliefs but also minimizes complexities and streamlines the fabrication process. It is recommended to choose a radius equal to or greater than the metal thickness for the best folds, especially when working with thicker metals. Additionally, avoiding unnecessary small bends can help reduce costs and simplify the fabrication process further.
Consistency in bending orientation is key to optimizing the fabrication workflow and ensuring a seamless bending operation, ultimately contributing to the success of the steel fabrication project.
Simplified Folds
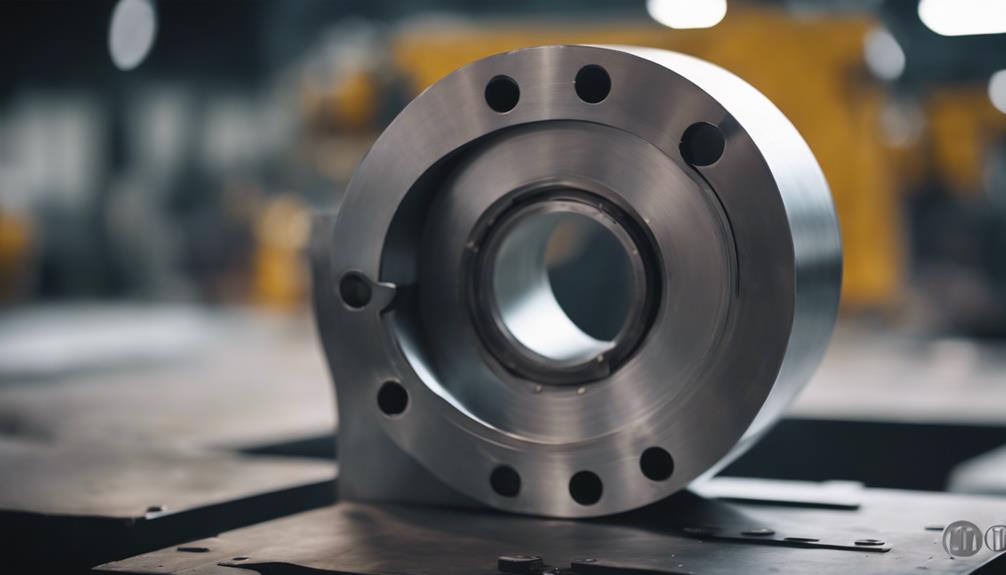
For enhanced cost-effectiveness and efficiency in sheet metal fabrication, simplifying folds is a strategic approach that can lead to significant savings. When choosing a radius equal to or greater than the metal thickness for bends, the result is better folds that are more cost-effective.
It is important to note that small bends on thick parts are less accurate and can actually increase fabrication costs. Additionally, complicated designs with multiple angles in bends can escalate project expenses due to the increased complexity involved.
Specific Clearances
Proper adherence to specific clearances plays a vital role in ensuring the structural integrity and longevity of components in industrial steel fabrication projects. Maintaining a minimum clearance of 1.5 times the material thickness between a hole and a bend is essential to prevent distortion during the fabrication process. These specific clearances are not arbitrary; they are designed to uphold material integrity and prevent issues such as cracking that can occur when clearances are not followed accurately.
Adhering to clearance guidelines goes beyond just preventing distortion; it greatly enhances the structural strength and durability of fabricated components. By ensuring that the correct clearances are maintained, the risk of material deformation or failure at connection points is reduced, contributing to the overall quality of the steel fabrication project.
Understanding and implementing specific clearances is fundamental for achieving precise and high-quality results in industrial steel fabrication, making it an indispensable aspect of the fabrication process.
Bend Reliefs
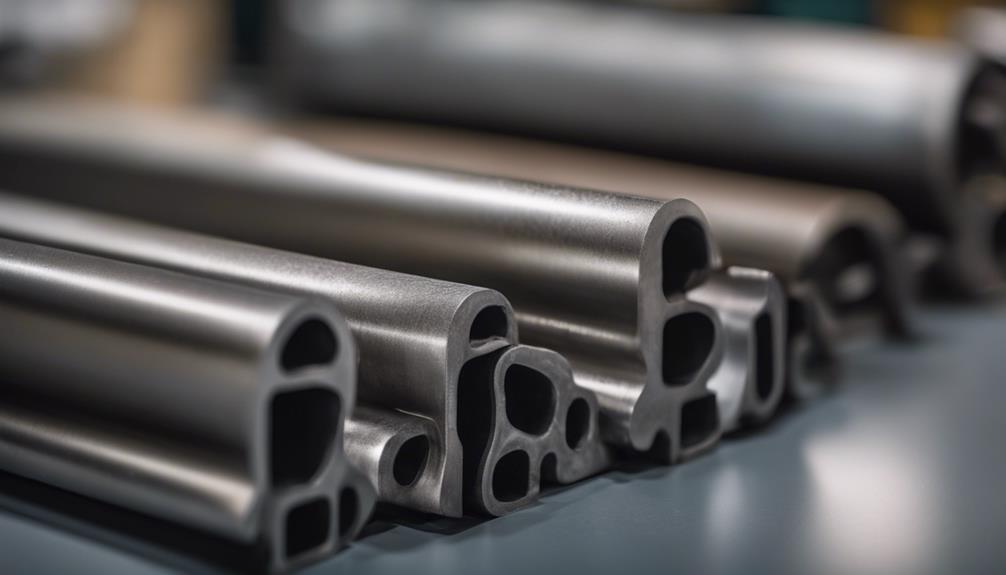
Bend reliefs play a crucial role in industrial steel fabrication projects, safeguarding against metal distortion or tearing during the bending process. By incorporating bend reliefs into the design of metal components, engineers can guarantee the structural integrity and quality of the final product.
These features are strategically placed to help maintain the material’s strength by preventing stress concentrations that could lead to failure. The size and shape of bend reliefs are carefully calculated based on factors such as material thickness and bending requirements.
Proper utilization of bend reliefs not only reduces the likelihood of defects but also enhances the overall durability of fabricated metal parts. Manufacturers rely on the implementation of bend reliefs to mitigate the risks associated with bending processes, ultimately contributing to the production of high-quality steel components that meet stringent industry standards.
Cost-Effective Strategies
To enhance cost efficiency in industrial steel fabrication projects, implementing strategic measures can lead to significant savings without compromising quality. Utilizing standard stock sizes can result in savings of up to 20% on metal costs by minimizing material waste and processing time.
Avoiding excessive tight tolerance call-outs is another cost-effective strategy as it reduces the need for precision machining, thereby lowering overall production expenses. Opting for thinner, more pliable metals can also contribute to cost savings since thicker materials may increase fabrication complexity and limit bending angles, leading to higher manufacturing costs.
Keeping bends in the same orientation and simplifying folds and angles in bends are additional ways to reduce expenses in industrial steel fabrication projects by streamlining production processes and minimizing the need for additional steps. By incorporating these cost-effective strategies, project managers can effectively manage expenses while maintaining the desired quality standards.
Quality Enhancement
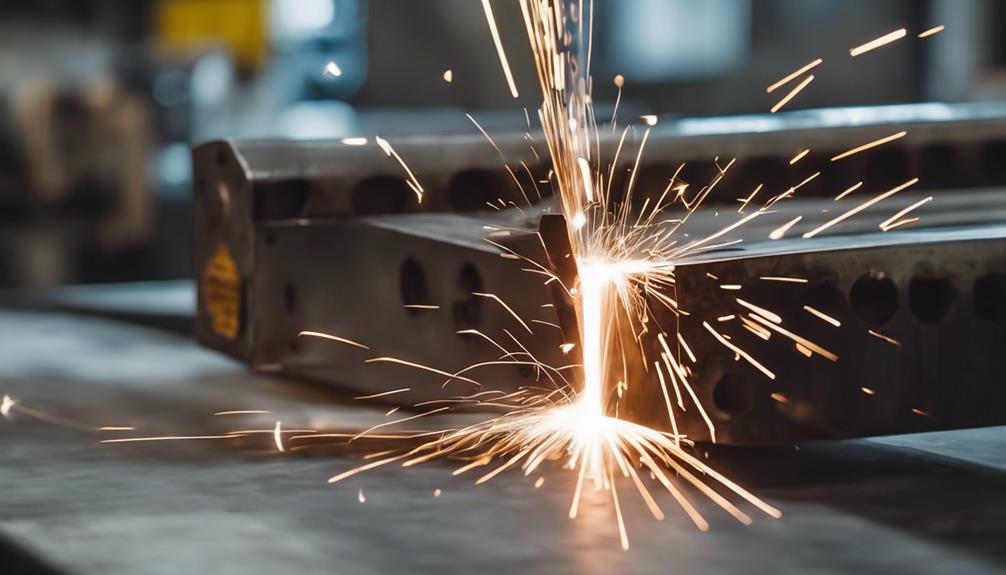
Ensuring the highest standards of precision and accuracy is paramount in enhancing the quality of industrial steel fabrication projects. Quality enhancement in this field involves meticulous attention to detail, including precise cuts, accurate welds, and proper shaping techniques. Advanced technology, such as CNC machines, plays a pivotal role in improving the accuracy and efficiency of fabrication processes.
Rigorous quality control measures are essential for detecting and rectifying any defects or imperfections that may arise during fabrication. Regular inspections throughout the fabrication process help guarantee that the final products meet project specifications and adhere to industry standards. By focusing on quality enhancement strategies, Industrial Steel Fabrication projects aim to deliver durable, reliable, and high-quality steel products suitable for a wide range of industrial applications. Emphasizing quality not only meets client expectations but also contributes to the overall success and reputation of the project.
Adherence to Guidelines
Maintaining strict adherence to industry guidelines is essential for ensuring the quality, precision, and safety of industrial steel fabrication projects. Adherence to guidelines guarantees compliance with safety standards and regulations, reducing the risk of workplace accidents and ensuring the well-being of workers.
Following specific fabrication procedures is vital as it not only ensures product quality but also guarantees precision in the final output. Additionally, compliance with project specifications and requirements is key for achieving successful outcomes that meet client expectations. Adhering to design guidelines plays a significant role in preventing errors and rework, ultimately saving valuable time and resources.
Meeting structural standards and material specifications is paramount for the success of industrial steel fabrication projects, as deviations from these guidelines can compromise the structural integrity and overall quality of the final product. By strictly adhering to industry guidelines, fabricators can uphold the highest standards of excellence in their projects.
Frequently Asked Questions
What Are the 9 Ways to Better Fabrication?
Understanding material properties, equipment selection, quality control, employee training, and collaboration with experienced fabricators are key factors for enhancing fabrication outcomes. These facets contribute to improved efficiency, precision, safety, and overall success in industrial steel fabrication projects.
What Are the 3 Main Fabrication Techniques?
The three main fabrication techniques are cutting, forming, and welding. Cutting involves processes like shearing, sawing, or chiseling. Forming includes bending, rolling, and stamping. Welding joins metal pieces using techniques like MIG, TIG, or stick welding.
What Are the Basics of Steel Fabrication Process?
The basics of the steel fabrication process involve cutting, bending, and welding steel sheets to create structures and products. Tools such as laser cutting equipment, plasma cutters, and welding machines are essential, along with skilled workers and specialized equipment for quality results.
What Is the Most Important Quality in a Fabricator?
Expertise is the most critical quality in a fabricator, ensuring high-quality steel fabrication. Skilled professionals demonstrate precision in metal cutting, bending, and welding. Attention to detail, problem-solving skills, and a reputation for on-time, on-budget delivery are also essential for project success.
Conclusion
To sum up, successful industrial steel fabrication projects necessitate careful consideration of:
- Material selection
- Design tolerances
- Stock gauges
- Uniform bends
- Simplified folds
- Bend reliefs
- Cost-effective strategies
- Quality enhancement
- Adherence to guidelines
By following these top 10 tips, companies can guarantee efficient and effective fabrication processes that meet the highest standards of quality and precision.