Steel product manufacturing entails a process starting with sourcing iron ore, coal, and scrap steel globally. These raw materials are processed in plants for optimization. Melting and casting involve recycling steel in furnaces, then continuous casting into beams and shapes. Rolling techniques refine steel properties through hot and cold processes. Heat treatment alters steel properties while machining creates precise components. Surface finishing enhances appearance and durability. Cleaning and coating techniques prepare steel for various applications. The industry uses steel for construction, automotive, and more, known for its durability and versatility. Discover the intricate journey from raw materials to finished steel goods.
Key Takeaways
- Global sourcing of iron ore, coal, and scrap steel for production efficiency.
- Melting recycled steel in electric arc furnaces to reduce emissions.
- Hot and cold rolling techniques for shaping and improving properties.
- Heat treatment methods like annealing and quenching for altering steel properties.
- Surface finishing processes like galvanizing for corrosion resistance.
Raw Material Sourcing
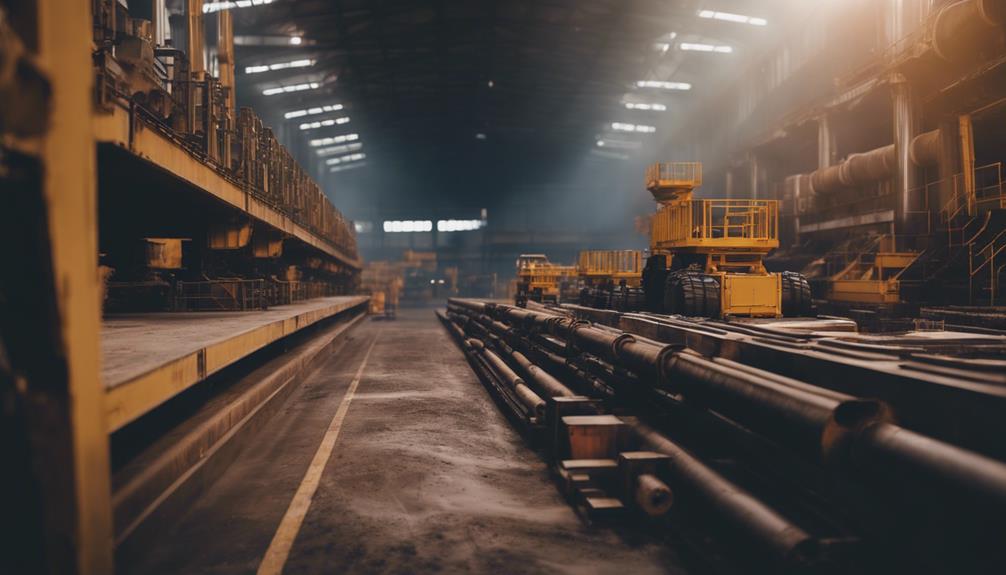
Raw material sourcing is a critical initial phase in the Steel Product Manufacturing Process, involving the global acquisition of key resources like iron ore, coal, and scrap steel through various mining operations. The steel manufacturing industry heavily relies on the efficient supply chain of these raw materials to guarantee uninterrupted production. Core drilling and haul trucks are commonly utilized techniques for the extraction and transportation of iron ore and coal, vital elements in steel production. Additionally, steel raw materials undergo processing, such as unloading with stacker/reclaimers in coking and sinter plants, to prepare for the manufacturing process.
Efficient raw material processing is paramount for the steel industry as it ensures a steady and reliable supply chain for manufacturing finished steel products. By optimizing the sourcing and processing of raw materials, steel manufacturers can enhance production efficiency, reduce costs, and meet the demands of the market effectively. A well-organized raw material sourcing strategy sets the foundation for a successful steel manufacturing operation.
Steel Scrap Melting
In the steel manufacturing process, the transformation of recycled steel through the melting of steel scrap in electric arc furnaces stands as a crucial stage, driving resource efficiency and environmental sustainability. Steel scrap melting is a critical step that helps reduce the dependence on raw materials by utilizing recycled steel.
Electric arc furnaces are the primary method used for this process, relying on high-power electric arcs to generate the intense heat required to melt the steel scrap effectively. This approach not only aids in energy efficiency but also contributes to a reduction in greenhouse gas emissions compared to traditional steelmaking methods.
By melting scrap steel in electric arc furnaces, manufacturers can produce liquid steel, which serves as the foundation for creating a wide range of steel products.
Casting Into Various Shapes
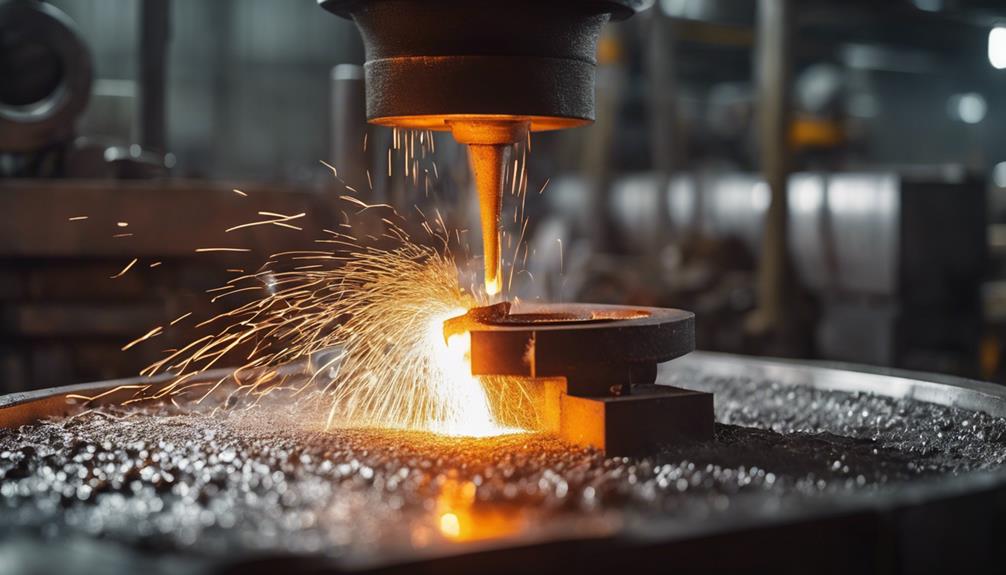
How is steel transformed into various shapes like beams, slabs, and billets in the steel manufacturing process through the casting method?
The answer lies in the technique of continuous casting. In this process, molten steel is poured into cooled molds and then drawn out using guided rollers to allow for the steel to harden and solidify. By cutting the cooled and solidified steel into desired lengths, different steel shapes such as beams, slabs, and billets are obtained. Casting plays an important role in the steel manufacturing process as it gives steel its initial shape and form, setting the foundation for further processing and finishing.
Continuous casting stands out for its efficiency in the production of steel shapes. It enables a continuous flow of steel shapes to be created, allowing for seamless and efficient production. This method ensures that the steel shapes produced are of high quality and can undergo subsequent processes with ease. Continuous casting contributes significantly to the overall efficiency and productivity of steel manufacturing operations.
Hot Rolling Process
The hot rolling process in steel manufacturing involves heating the steel above its recrystallization temperature and passing it through rollers to achieve desired shapes. This method is crucial for reducing the thickness of steel slabs or ingots, leading to improved mechanical properties and surface finish.
By shaping steel into products like sheets, plates, and coils during hot rolling, manufacturers prepare the material for further processing in various industries. The high temperatures used in hot rolling play a significant role in creating a uniform grain structure, ultimately enhancing the overall strength of the steel produced.
This process is essential in steel production as it enables the creation of a wide range of products used in construction, automotive manufacturing, and other industrial applications. Hot rolling stands as a foundational step in the steel manufacturing process, ensuring that the steel meets the necessary standards for quality, durability, and functionality.
Cold Rolling Techniques
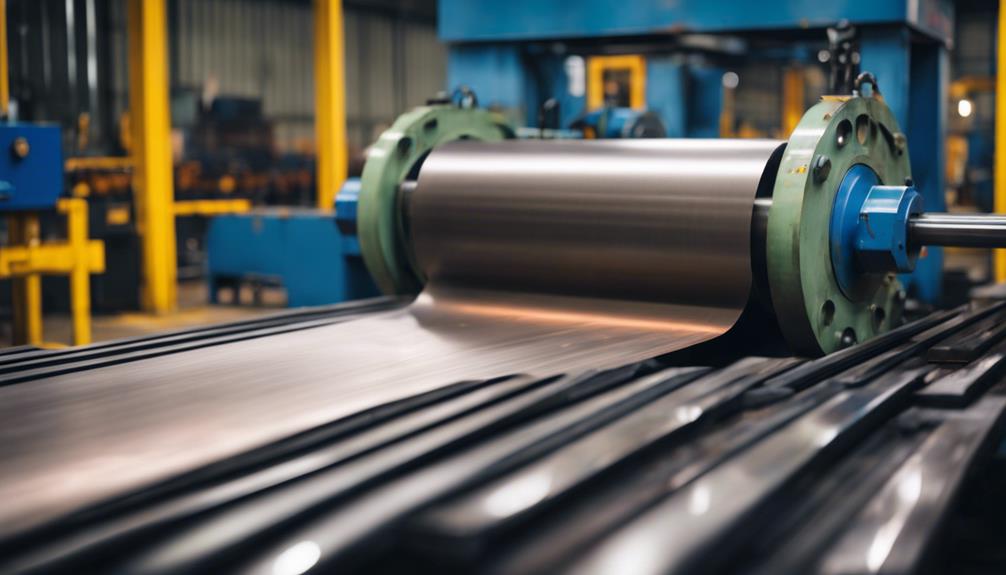
Utilizing cold rolling techniques, steel sheets or coils undergo a process at room temperature to precisely reduce their thickness and enhance their mechanical properties and surface characteristics. The cold rolling process involves passing the steel through a series of rollers that exert pressure to decrease the thickness while maintaining tight dimensional tolerances. This method results in improved surface finish, high strength, and excellent uniformity across the steel product.
Steel sheets produced through cold rolling find extensive use in various industrial applications due to their superior qualities. Industries such as automotive manufacturing, construction, and appliance production benefit from cold-rolled steel sheets’ precise thickness control and enhanced mechanical properties. These sheets can be manufactured as thin as 0.05mm, making them suitable for applications requiring thin yet strong materials, such as automotive body panels. The superior surface quality and dimensional accuracy offered by cold-rolled steel make it a preferred choice in industries that demand high-quality steel products.
Heat Treatment Methods
In steel manufacturing processes, heat treatment methods play an essential role in altering the material’s properties to meet specific requirements. These methods include annealing, quenching, and tempering.
Annealing is a process where steel is heated to a specific temperature and then slowly cooled to relieve internal stresses and increase ductility.
Quenching involves rapid cooling of the steel to trap carbon atoms within the crystal lattice, resulting in hardened steel. Following quenching, tempering is carried out to reduce the brittleness of the steel while maintaining its hardness and strength.
By carefully controlling the heating and cooling processes involved in these treatments, manufacturers can achieve the desired mechanical properties in the steel, making it suitable for various applications.
Additionally, hardening is another heat treatment method used to increase the hardness of steel by heating it to a critical temperature and rapidly cooling it. These methods are pivotal steps in producing steel products with the required strength, toughness, and durability.
Cutting and Machining Processes
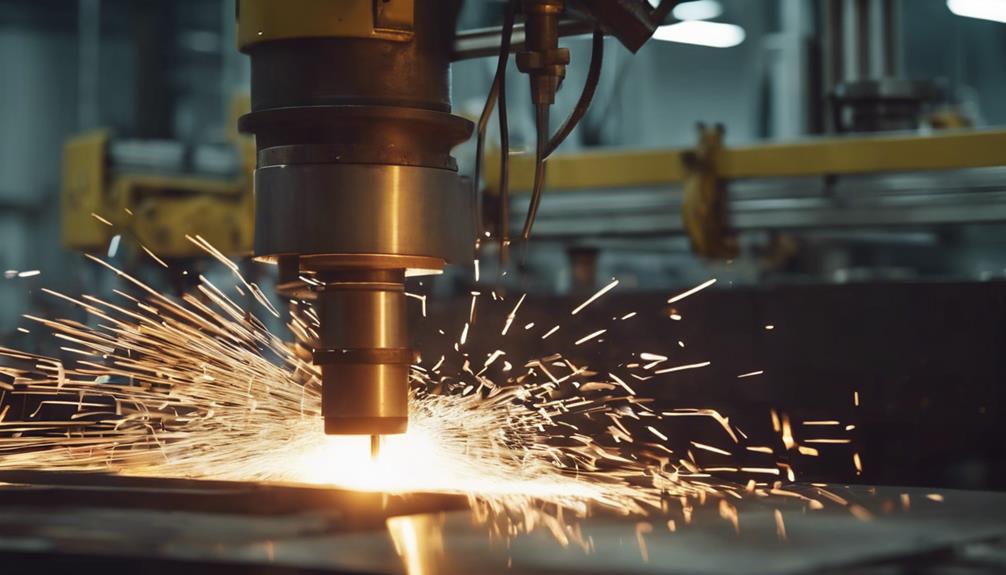
Within steel manufacturing processes, the cutting and machining operations are important for shaping and creating precise components from steel materials. Cutting processes like sawing, shearing, and plasma cutting are utilized to shape steel into desired sizes, while machining processes such as milling, drilling, and turning are used to create precise shapes and holes in steel components.
Computer Numerical Control (CNC) machines play a significant role in steel manufacturing, offering accurate and automated cutting and machining operations. CNC machines guarantee efficiency and consistency in producing steel parts to exact specifications. Laser cutting technology is also widely used for its high precision in cutting steel sheets and plates for various industrial applications.
Expertise is essential in machining processes to guarantee the dimensional accuracy and surface finish of the final steel products, meeting quality standards and functional requirements in the steel manufacturing industry.
Surface Finishing Techniques
Surface finishing techniques play a pivotal role in enhancing the quality and functionality of steel products by improving their appearance and properties.
Shot blasting is a process where abrasive materials are propelled at high speeds onto the steel surface to eliminate rust, scale, or contaminants, preparing it for further treatment.
Pickling, on the other hand, involves treating the steel surface with acids to remove oxide layers, scale, and impurities, resulting in a clean and smooth surface for subsequent finishing.
Electroplating is a method that deposits a thin layer of metal, such as zinc or nickel, onto the steel surface through electrolysis to enhance corrosion resistance, appearance, or conductivity.
These techniques are essential in improving the durability, aesthetics, and functionality of steel products across various industries like construction, automotive, and manufacturing. Each method serves a specific purpose in ensuring that steel products meet the required standards for their intended applications.
Quality Control Measures
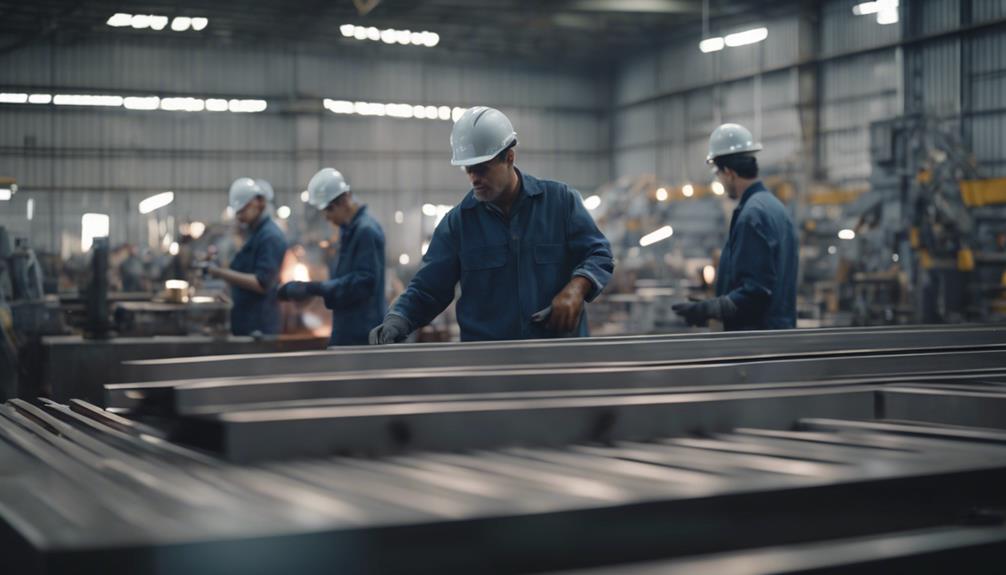
Quality control measures are essential components of the steel manufacturing process, ensuring the consistency, purity, and reliability of raw materials and final steel products. Raw materials testing plays a vital role in quality control, with iron ore, coal, and scrap steel undergoing rigorous analysis for purity and consistency. Technologies like spectroscopy and X-ray fluorescence are employed to assess the chemical composition of raw materials, ensuring quality assurance throughout the manufacturing process.
In addition to raw materials testing, quality control in steel production involves continuous monitoring of temperatures, pressures, and chemical reactions to maintain the desired properties of the steel. Various inspection methods such as dimensional inspections, non-destructive testing, and visual inspections are implemented at different stages to identify any defects or inconsistencies in the steel products. These measures are in place to meet industry standards, specifications, and customer requirements, ultimately delivering reliable and high-quality steel products to the market.
Industry Applications
The widespread utilization of stainless steel across various industries underscores its exceptional durability, corrosion resistance, and versatility in meeting diverse application requirements.
In the construction sector, stainless steel is favored for structural elements and cladding due to its durability and resistance to corrosion, ensuring longevity and structural integrity in buildings.
Within the food industry, stainless steel is the material of choice for kitchen equipment and utensils, thanks to its hygienic properties and ease of cleaning, meeting strict hygiene standards essential for food preparation.
The automotive industry benefits from stainless steel in exhaust systems and trim components, as it offers resistance to high temperatures and corrosion, enhancing the longevity and performance of these parts.
The versatility of stainless steel extends to various industries, including construction, food, and automotive, showcasing its adaptability and reliability in meeting the demanding requirements of different applications.
Frequently Asked Questions
What Is the Process of Manufacturing Steel Products?
The process of manufacturing steel products involves converting raw materials like iron ore into molten iron through methods like blast furnace. Refining the molten iron into raw steel via techniques like Basic Oxygen Steelmaking or Electric Arc Furnace, followed by shaping, treatment, and coating for final products.
What Is the Steel Making Process From Start to Finish?
The steel making process from start to finish involves melting iron ore, coal, and lime to produce molten iron, removing impurities through techniques like BOS or EAF, treating the raw steel for desired grades, continuous casting, and secondary forming processes like heat treatment and coating.
How to Manufacture a Steel Product?
To manufacture a steel product, raw materials like iron ore and coal are converted into liquid iron through furnaces. This liquid iron is then processed into steel using methods like oxygen and arc furnaces. Shaping, rolling, and finishing processes follow to create various steel products.
What Are the Methods of Production of Steel?
Steel production methods include basic oxygen steelmaking (BOS), electric arc furnace (EAF), and direct reduced iron (DRI) processes. These methods utilize various techniques like oxygen blowing, electric arcs, and reduction by natural gas or coal to produce high-quality steel products efficiently.
Conclusion
To sum up, steel product manufacturing involves a series of processes from raw material sourcing to the production of finished goods. These processes include:
- Steel scrap melting
- Casting into various shapes
- Hot and cold rolling techniques
- Cutting and machining processes
- Surface finishing techniques
- Quality control measures
The industry applications of steel products are vast and essential across various sectors such as construction, automotive, infrastructure, and manufacturing.