Strategic planning and efficient design are vital in warehouse construction. Considerations such as space utilization, automation integration, future growth, and employee well-being play pivotal roles. Sustainable practices and regulatory adherence are also essential. These factors guarantee warehouses are not just functional today but also future-proofed for tomorrow, setting the stage for long-term business success.
Key Takeaways
- Strategic facility planning optimizes space utilization for future growth.
- Automation integration enhances labor efficiency and productivity.
- Designing for flexibility and adaptability prepares for operational changes.
- Employee safety and comfort are prioritized in warehouse design.
- Sustainable practices and green initiatives reduce environmental impact.
What is the Steel Structure of a Warehouse?
The steel structure of a warehouse provides essential support and stability for the building. It typically consists of steel columns, beams, and roof trusses. Columns are vertical members that bear the weight of the structure and transfer it to the foundation. Beams are horizontal members that connect the columns, providing additional support. Roof trusses are triangular structures that support the roof and distribute its weight evenly. Steel is preferred for warehouse construction due to its strength, durability, and cost-effectiveness. It allows for large, open interior spaces without the need for numerous supporting columns, making it ideal for storage and industrial purposes.
Steel Warehouse Facility Design and Space Utilization
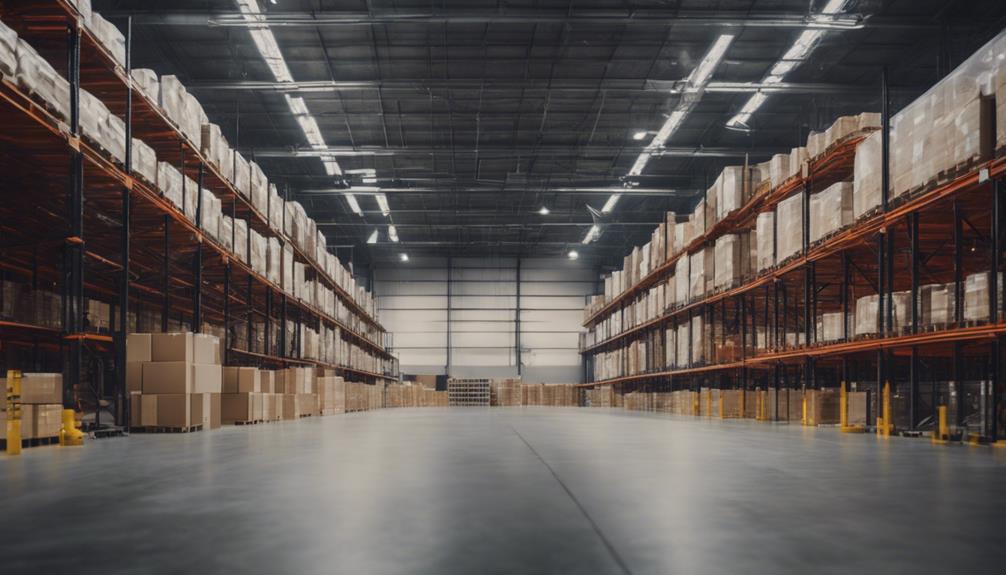
How can strategic facility planning optimize warehouse space utilization effectively in response to evolving operational demands and labor challenges? Warehouse construction companies play an essential role in addressing this question by designing facilities that are not only efficient in space utilization but also adaptable to changing needs. By working closely with warehouse construction companies that specialize in creating innovative and flexible spaces, businesses can guarantee that their warehouses are equipped to handle evolving operational demands and labor challenges.
These companies understand the importance of right-sizing warehouses and considering future growth to avoid wasted space or the need for frequent expansions. By designing for flexibility and adaptability, warehouse construction companies enable businesses to make efficient use of their space while also being prepared for any changes in operations or storage requirements.
Additionally, by prioritizing employee safety, comfort, and recruitment through thoughtful facility design, warehouse construction companies contribute to creating a conducive and attractive work environment that can help address labor challenges effectively.
Automation Integration and Labor Efficiency
Integrating automation systems into warehouse operations is a pivotal strategy for enhancing labor efficiency and optimizing overall productivity. By incorporating advanced technologies such as robotics and AI, warehouses can greatly reduce labor costs by up to 70% and achieve up to a 30% savings in operational expenses. Automated systems have shown to improve picking efficiency by 2-3 times compared to manual processes, allowing for faster order fulfillment and increased throughput. Additionally, these technologies can handle up to 80% of repetitive tasks, freeing up employees to focus on more value-added activities.
When considering warehouse construction materials, it is essential to plan for the integration of automation systems to guarantee seamless operation and maximize utilization of space. Investing in durable materials that can support the installation of robotic equipment and conveyors is vital for long-term efficiency. By incorporating automation into the design and construction process, warehouses can experience a 15-20% increase in productivity while creating a more streamlined and cost-effective operation.
Future Growth and Adaptability Planning
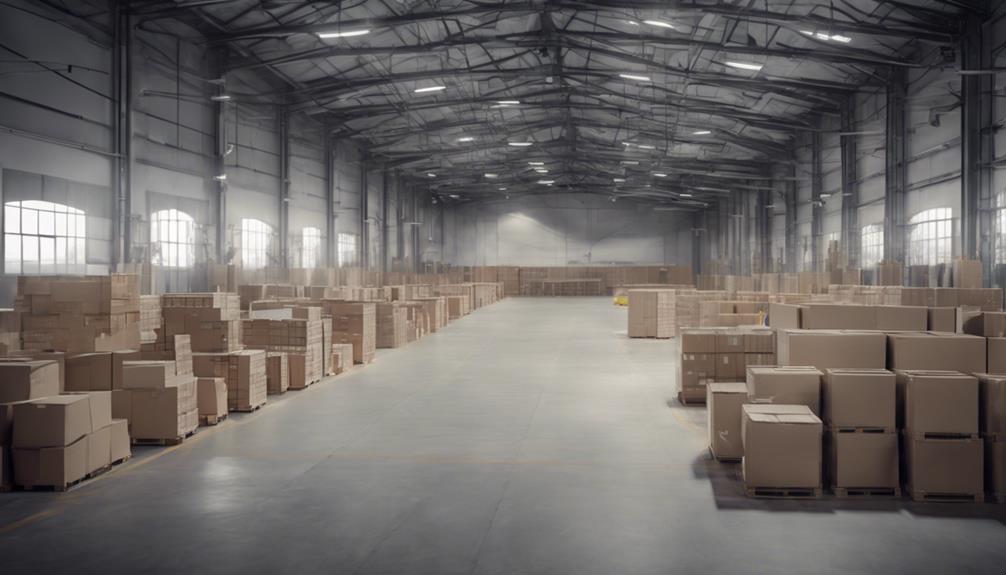
Guaranteeing future growth and adaptability in warehouse construction requires careful planning and design considerations to accommodate evolving business needs effectively. Warehouse construction firms play a crucial role in verifying sites for potential growth, allowing for scalability and adaptability.
By designing with growth flexibility in mind, these firms enable easy expansion and modification of facilities as business requirements change over time. Additionally, planning for niche functions and specialized facilities from the outset ensures that warehouses can cater to diverse operational needs efficiently.
Through upfront planning for all facility uses, warehouse construction firms can optimize space and functionality to support long-term growth objectives. Insights from projects like RS&H highlight the importance of incorporating cold storage capabilities and expansion planning strategies into sustainable warehouse development, further underscoring the significance of future growth and adaptability planning in the construction process.
Employee Safety and Comfort Prioritization
In order to guarantee a safe and comfortable working environment, warehouse construction must prioritize employee safety and well-being through thoughtful design considerations. Designing for employee safety involves intricate egress layouts in larger facilities and considering how the placement of equipment affects egress distances.
Break and rest areas are essential in warehouse design to enhance employee comfort and overall well-being. Foresight in building functionality is important to address the specific safety and comfort needs of employees. Additionally, meeting FDA requirements for temperature control is necessary, as it directly impacts warehouse design to guarantee employee safety.
Sustainable Practices and Green Initiatives

Sustainable practices and green initiatives play an essential role in modern warehouse construction, emphasizing environmental responsibility and resource efficiency. Incorporating energy-efficient lighting is a key aspect of green initiatives in warehouse design. By using energy-efficient lighting solutions, warehouses can greatly reduce their energy consumption and carbon footprint. Additionally, utilizing low embodied carbon solutions and efficient HVAC systems further contribute to environmental sustainability in warehouse operations.
Another sustainable practice is the strategic location of warehouses in urban settings to reduce transportation needs and promote a closer proximity to the workforce, decreasing overall carbon emissions. Furthermore, incorporating green features in warehouse design, such as green spaces and biodiversity initiatives, not only enhances the environmental impact but also promotes a healthier work environment for employees.
Structural considerations like material selection for sustainability, fire safety measures, and load resistance are vital aspects of sustainable warehouse design, ensuring long-term environmental conservation and operational efficiency. By integrating these sustainable practices and green initiatives, warehouses can build for the future with a strong focus on environmental stewardship and energy efficiency.
Compliance and Regulatory Considerations
Adhering to building codes and regulatory standards is paramount in warehouse construction to guarantee safety and compliance with legal mandates. When initiating a warehouse construction project, a warehouse construction company must ensure strict adherence to various regulatory considerations. These include meeting fire safety standards to protect the premises and its occupants, establishing occupancy limits to prevent overcrowding, and incorporating accessibility requirements to accommodate individuals of all abilities.
Moreover, understanding zoning laws and environmental regulations is essential to avoid potential delays and legal complications during the construction process. Compliance with Occupational Safety and Health Administration (OSHA) regulations is also a top priority for warehouse construction companies to safeguard the well-being of employees and mitigate the risk of penalties.
Additionally, obtaining the necessary building permits and approvals in alignment with local, state, and federal regulations is imperative before commencing any warehouse construction to ensure a smooth and legally compliant project execution.
To wrap up, warehouse construction necessitates meticulous deliberation of facility design, automation integration, future growth planning, employee safety, sustainable practices, and regulatory compliance. By prioritizing these crucial elements, companies can construct warehouses that are efficient, adaptable, and safe for their employees.
It is essential to incorporate these considerations into the construction process to guarantee long-term success and sustainability in the ever-evolving warehouse industry.
Frequently Asked Questions on Steel Warehouse Construction
What are the Considerations for Warehouse Construction?
Considerations for warehouse construction encompass optimizing operational efficiency, storage capacity, accessibility, throughput, and product specifications. Financial evaluations, safety regulations compliance, and site details play an essential role. Efficient inventory management, order fulfillment, and workflow streamlining are crucial.
What Must Be Taken in Consideration Before Building a New Warehouse?
Before constructing a new warehouse, conduct a needs assessment to determine storage requirements, budget, and goals. Plan a logical flow of operations to optimize efficiency. Allocate space wisely, considering throughput, product specifications, and operational needs for maximum functionality and capacity.
What is the Future of Warehousing?
The future of warehousing involves automation, technology integration, and sustainability practices to enhance efficiency and reduce costs. Warehouses prioritize space optimization, growth flexibility, and employee safety through innovative design, incorporating energy-efficient systems and eco-friendly materials.
What are the Factors to Be Considered in Setting up a Warehouse?
Factors in setting up a warehouse include design for operational flow, accessibility for handling, efficient space allocation, throughput evaluation based on product characteristics and volumes, and understanding product specifications for storage needs. These elements guarantee operational efficiency.