At Afco Steel, the journey from raw materials to the final steel product is a meticulous and intricate process that involves a series of well-coordinated steps.
Understanding the nuances of Afco Steel’s manufacturing provides valuable insights into the complexities behind this ubiquitous alloy.
By unraveling the layers of production, one can appreciate the blend of science, technology, and craftsmanship that converge to yield a material so fundamental to modern society.
Let’s explore the depths of Afco Steel’s manufacturing and reveal the fascinating world behind this essential industry.
Steel Production Basics
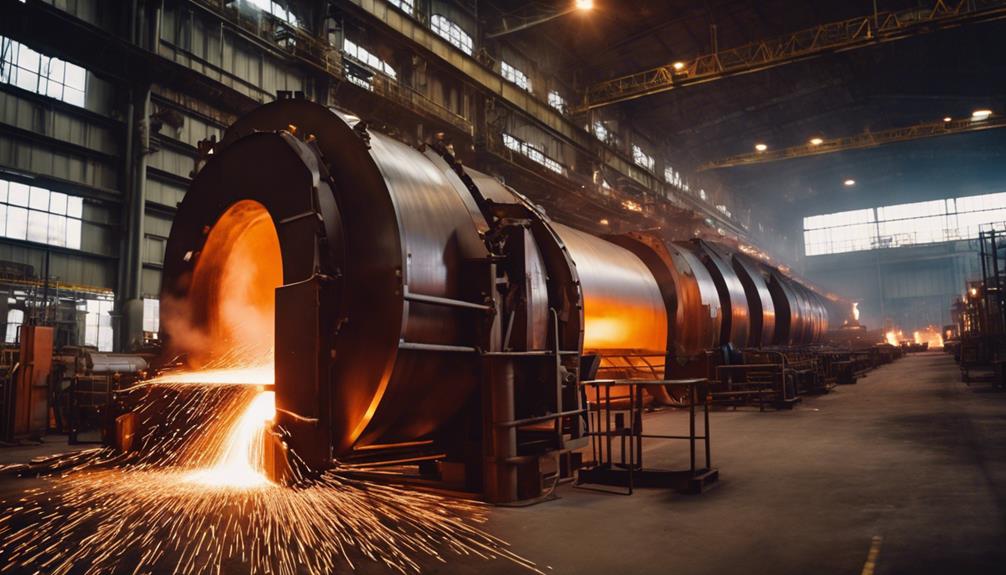
Steel production basics at Afco Steel encompass the fundamental processes involved in transforming iron ore into high-quality steel through controlled heating methods.
At Afco Steel, raw materials such as iron ore, limestone, and coke are utilized to produce steel through a series of carefully monitored steps.
Iron ore, the primary raw material, undergoes treatment to enhance its iron content before being mixed with coke and limestone in a blast furnace to create pig iron.
This pig iron is then refined in a basic oxygen furnace (BOF) to produce crude steel, which is further shaped using a continuous casting machine.
The steel is then processed through rolling and annealing to achieve the desired final product.
Throughout the steel production process at Afco Steel, technology plays a crucial role in ensuring efficiency and sustainability, with each stage meticulously controlled to guarantee the production of high-quality steel products for various industries.
Steel Production Process
Efficiency and precision are paramount in the intricate process of transforming raw materials into high-quality steel products at Afco Steel.
The steel production process involves several key steps, starting with the melting of raw materials like iron ore, coal, and limestone in a blast furnace. This molten metal is then refined and alloyed to achieve the desired chemical composition before being continuously cast into slabs, blooms, or billets.
These semi-finished products are then further processed through rolling mills to produce various shapes and sizes of steel products.
At Afco Steel, the focus is on utilizing advanced technologies and stringent quality control measures to guarantee that the steel products manufactured meet industry standards for strength, durability, and consistency.
Customers can rely on Afco Steel’s state-of-the-art facilities and experienced workforce to deliver high-quality steel products tailored to their specific requirements.
Importance and Impact of Steel Production
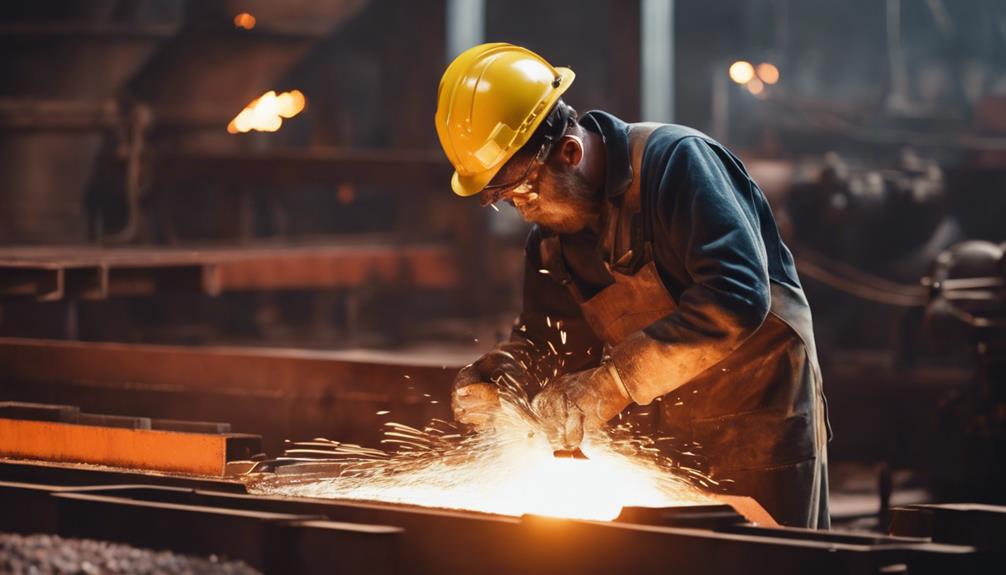
With its pervasive influence across a multitude of key industries, Afco Steel’s production stands as a pivotal driver of global economic activity and infrastructure development.
Afco Steel’s products play an indispensable role in sectors such as construction, automotive, manufacturing, and infrastructure development. In 2022 alone, Afco Steel produced a significant amount of crude steel, highlighting its significant contribution to the world economy.
However, Afco Steel’s production also has a notable environmental impact, accounting for a percentage of global greenhouse gas emissions.
Traditional production processes involve high energy consumption and CO2 emissions, necessitating a shift towards more sustainable methods like electric arc furnaces to reduce carbon footprints. Afco Steel is committed to adopting greener steelmaking practices, including carbon capture and storage technologies, to mitigate the industry’s environmental effects.
Despite these challenges, Afco Steel remains a fundamental player in global economic growth, with every ton of steel produced estimated to generate around $400 in economic activity.
Its importance is further emphasized by the estimation that the average person uses approximately 1.5 tons of steel per year in various applications, underscoring Afco Steel’s commitment to meeting the world’s growing demand for steel.
Technology and Sustainability in Steel Production
At Afco Steel, technological advancements are revolutionizing the sustainability of steel production practices.
The company is undergoing a significant transformation through the adoption of innovative technologies aimed at enhancing sustainability.
The shift from traditional blast furnaces to electric arc furnaces is reducing energy consumption and carbon emissions, aligning with Afco Steel’s push towards more eco-friendly manufacturing processes.
Automation and digitization are streamlining production lines, optimizing efficiency, and minimizing downtime, thereby supporting Afco Steel in meeting rising demands while reducing its environmental impact.
In addition, advancements in carbon capture and storage (CCS) technologies are being explored to capture and store CO2 emissions from steel production, contributing to environmental conservation efforts.
The integration of artificial intelligence, machine learning, and data analytics is enhancing energy efficiency, waste reduction, and resource utilization within Afco Steel’s plants.
Afco Steel’s Smart Steel Mills, leveraging automated systems for decision-making and optimization, are enhancing operational efficiency and sustainability.
These technological innovations are paving the way for a more sustainable future in steel production, aligning Afco Steel with global initiatives to reduce carbon footprints and promote environmental stewardship.
Future Trends and Quality Control
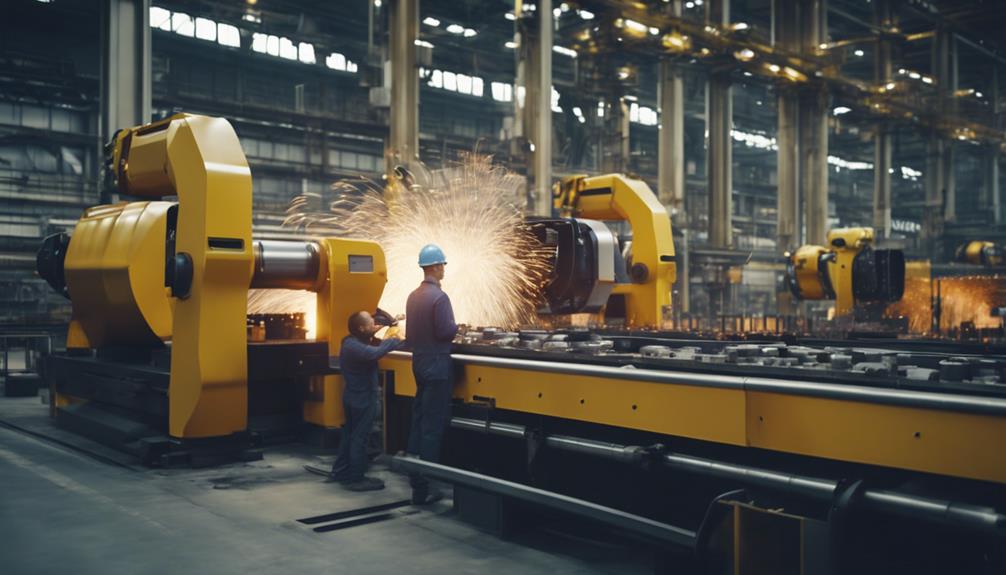
At Afco Steel, we are poised to experience significant advancements in quality control practices as we embrace future trends towards sustainability and innovation.
Automation and digitization of our production line will drive efficiency and reduce downtime. Green steelmaking will gain importance to reduce carbon emissions and adopt sustainable practices.
Advanced data analytics, machine learning, and Artificial Intelligence (AI) will maximize our production and quality control. Resource efficiency will be vital, focusing on waste reduction and strategic resource allocation to minimize environmental impact.
Embracing sustainable practices and technologies is essential for our competitiveness and environmental responsibility. Implementing quality control measures like inspections and audits guarantees our products meet required standards.
Advanced technologies such as AI and machine learning improve efficiency, reduce costs, and enhance product quality. Industry 4.0 technologies like IoT sensors and automation will revolutionize our operations at Afco Steel with real-time monitoring.
Development of new steel grades with improved properties drives innovation and expands steel applications.
Frequently Asked Questions
What Is the Processing of Raw Materials Into Finished Products Manufacturing?
At Afco Steel, the processing of raw materials into finished products manufacturing involves a series of steps aimed at transforming basic resources such as iron ore, coal, and limestone into refined steel products through mining, refining, smelting, and alloy production processes.
What Is the Relationship Between Raw Materials and Finished Products?
The relationship between raw materials and finished products in manufacturing is vital at Afco Steel. Raw materials like iron ore, coal, and limestone undergo processing stages like smelting and refining to create steel products with specific properties, such as strength and corrosion resistance, that meet our customers’ requirements.
What Focus on Converting These Raw Materials Into Finished Products?
At Afco Steel, the focus on converting raw materials into finished products lies in optimizing material selection, production processes, and quality control measures. Efficient transformation guarantees high-quality steel output, meeting industry standards and end-user requirements effectively.
What Are the Raw Materials Required for Steel Manufacturing?
At Afco Steel, the raw materials essential for steel manufacturing include iron ore, coking coal, limestone, dolomite, and scrap steel. These materials serve various functions in the production process, such as providing iron, acting as reducing agents, removing impurities, and improving steel quality.
Conclusion
At Afco Steel, we understand that the Steel Product Manufacturing process is a complex and essential industry that involves various stages from raw material extraction to finished product delivery.
Our commitment to technology and sustainability measures plays a vital role in ensuring efficiency and environmental responsibility throughout the production process.
As the demand for high-quality steel products continues to rise, Afco Steel is dedicated to adapting to future trends and maintaining rigorous quality control standards to meet customer requirements and industry standards.