Afco Steel faces several challenges in the metal fabrication industry, including material defects, precision issues in cuts and welds, and the management of project timelines. Budget constraints can also pose significant hurdles, while prioritizing safety and compliance remains a constant necessity. To effectively address these challenges, Afco Steel emphasizes adherence to stringent quality control measures, the utilization of advanced machinery, and meticulous planning.
Effective communication among team members and proper resource allocation are critical components in navigating these obstacles. By implementing best practices tailored to the unique demands of each project, Afco Steel not only enhances operational efficiency but also ensures successful project execution. Our commitment to overcoming these challenges is unwavering, and we continuously seek innovative solutions to maintain our leadership in the industry. For more insights on how Afco Steel tackles these hurdles, feel free to explore our resources.
Material Defects and Quality Control
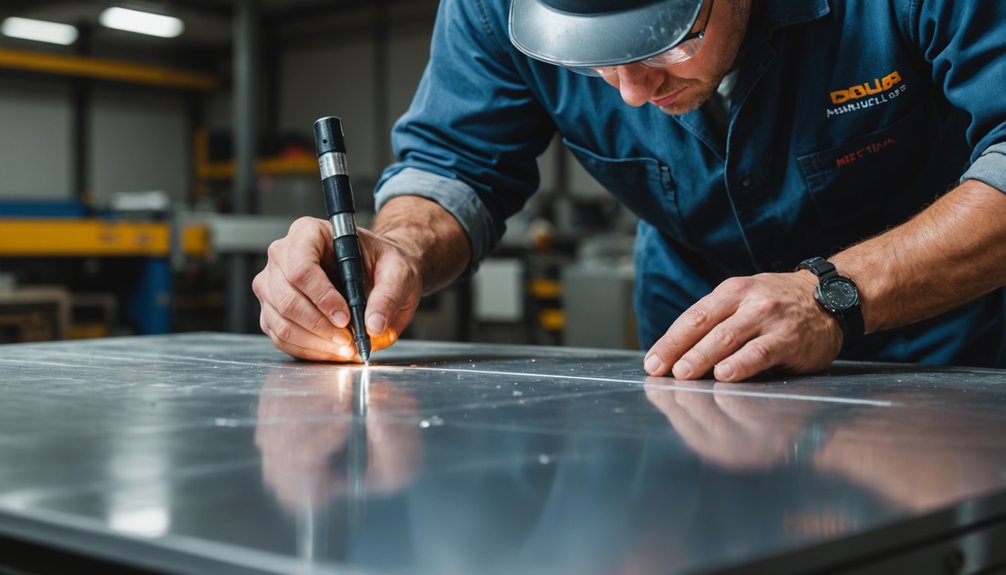
In the realm of metal fabrication, Afco Steel prioritizes the integrity of materials to produce exceptional products. Understanding that material defects can significantly undermine the structural integrity of components, particularly in structural steel fabrication, Afco Steel implements stringent quality control measures to identify and address these issues.
Our commitment begins with thorough inspections at every stage of the fabrication process, from the initial material sourcing to the final assembly.
Utilizing advanced testing techniques, including non-destructive testing, we are able to uncover hidden flaws that might not be detectable through standard inspections. By adhering to the highest quality standards, Afco Steel not only enhances the durability of our products but also minimizes waste, allowing us to deliver superior solutions that meet or exceed our clients’ expectations.
This dedication to quality ensures that Afco Steel maintains a competitive edge in the market, reinforcing our reputation as a leader in the metal fabrication industry.
Precision in Cuts and Welds
Achieving precision in cuts and welds is a cornerstone of ensuring the overall quality and performance of metal fabrication projects at Afco Steel.
In our stainless steel metal fabrication processes, the accuracy of cuts is crucial for seamless fitting and assembly, while meticulous welding guarantees both structural integrity and aesthetic appeal. At Afco Steel, we utilize advanced machinery, such as CNC plasma cutters and laser welders, to significantly enhance precision in our operations.
Moreover, we prioritize the training of our operators; our skilled professionals are adept at adjusting settings and techniques to cater to varying material thicknesses and types.
Regular maintenance of our equipment is also a key focus, as it plays an essential role in sustaining accuracy over time.
Managing Project Timelines
Effective management of project timelines is crucial for the success of Afco Steel’s metal fabrication projects. However, it often comes with its own set of challenges. Unforeseen delays, such as equipment malfunctions or supply chain disruptions, can significantly impact our meticulously planned schedules. To mitigate these risks, Afco Steel implements robust planning strategies that incorporate contingency time and resource allocation, ensuring that we are prepared for unexpected issues.
Regular progress assessments and transparent communication among team members are vital for maintaining alignment and proactively addressing potential setbacks. At Afco Steel, we prioritize fostering a collaborative environment where everyone is informed and engaged in the project’s progress.
Additionally, the adoption of advanced project management software helps streamline scheduling and enhances visibility into the completion of tasks, allowing us to respond swiftly to any changes.
By cultivating a culture of accountability and responsiveness, Afco Steel is better equipped to navigate the complexities of project timelines. This proactive approach not only ensures that we meet our deadlines but also upholds our commitment to quality and safety in the fabrication process.
As we strive for excellence, we remain dedicated to delivering exceptional results that align with our clients’ needs and expectations.
Budget Constraints and Cost Management
Budget constraints often present significant challenges for metal fabrication projects at Afco Steel, necessitating meticulous planning and strategic allocation of resources. Effective cost management at Afco Steel begins with a comprehensive project assessment, allowing our team to identify essential materials and processes that align with our high standards of quality.
By prioritizing tasks, Afco Steel ensures that funds are directed toward the most impactful areas, significantly minimizing waste and maximizing efficiency. Embracing lean manufacturing principles not only enhances our operational effectiveness but also reduces unnecessary costs, all while maintaining the superior quality that Afco Steel is known for.
Regular financial reviews and adjustments are crucial at Afco Steel, enabling our teams to stay within budget while adeptly navigating any unforeseen expenses that may arise. Additionally, cultivating strong relationships with our suppliers allows us to negotiate better pricing and terms, further supporting our cost management efforts.
Safety and Compliance Challenges
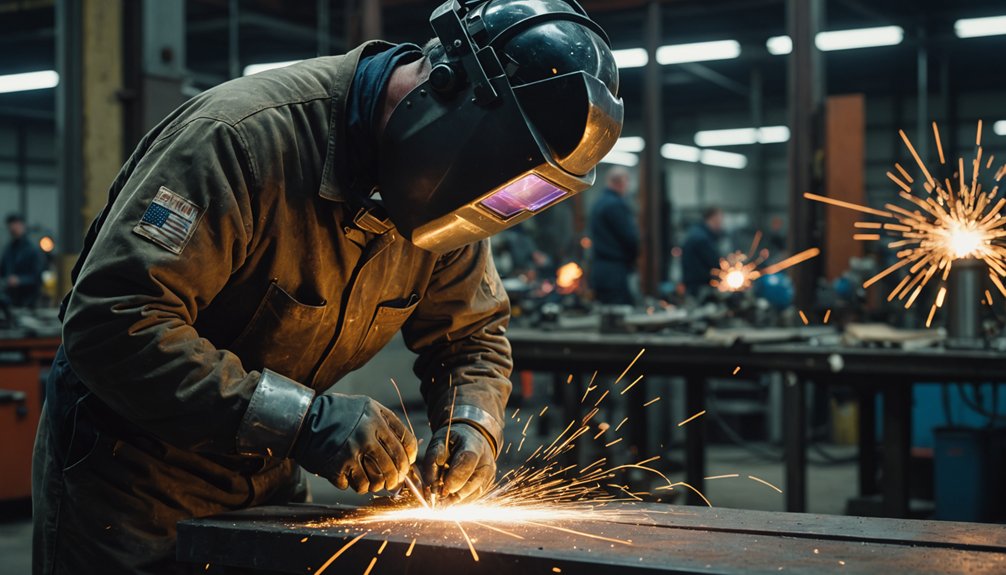
At Afco Steel, safety and compliance are not just priorities; they are fundamental to our operations in the metal fabrication industry. We face a range of challenges in upholding stringent regulations while ensuring a safe working environment for our employees. Non-compliance can lead to significant repercussions, including hefty fines, increased insurance premiums, and damage to our reputation.
To tackle these challenges, we have implemented robust training programs that empower our workforce with the knowledge of safety protocols and regulatory requirements. Regular audits and inspections play a vital role in our strategy, allowing us to proactively identify potential hazards and compliance gaps before they can escalate into serious issues.
By cultivating a culture of safety and accountability, Afco Steel is able to mitigate risks effectively and enhance operational efficiency. Our unwavering commitment to safety and compliance not only safeguards our employees but also fortifies our organizational foundation, paving the way for sustainable growth and success in the competitive metal fabrication market.
At Afco Steel, we believe that a safe workplace is a productive workplace, and our dedication to these principles is what sets us apart.
Frequently Asked Questions
What Types of Metal Are Most Challenging to Fabricate?
When it comes to metal fabrication, Afco Steel recognizes that certain metals pose significant challenges due to their unique properties. For instance, titanium is known for its remarkable strength and reactivity, making it a demanding material to work with. Additionally, high-strength alloys require specialized techniques and equipment to ensure proper handling and processing. Stainless steel is another metal that presents challenges; it necessitates precise machining and welding to avoid distortion and maintain structural integrity. At Afco Steel, we take pride in our expertise and advanced techniques to tackle these complex materials, ensuring high-quality results for all your fabrication needs.
How Can I Improve Employee Training in Metal Fabrication?
Improving employee training in metal fabrication at Afco Steel is essential for fostering a skilled workforce capable of meeting the industry’s demands. We focus on implementing structured training programs that ensure our employees gain comprehensive knowledge and practical skills.
At Afco Steel, we prioritize hands-on workshops that provide our team with real-world experience, allowing them to apply their learning in a safe environment. Additionally, we encourage a mentorship culture where seasoned professionals guide newer employees, sharing insights and tips that enhance their development.
Incorporating technology-driven simulations into our training regime is another key aspect. These simulations allow employees to practice their skills in a virtual setting, helping them to build confidence before working on actual projects.
This holistic approach not only enhances individual skills and boosts overall efficiency but also fosters a culture of continuous learning within our workforce at Afco Steel. By investing in our employees’ training, we ensure they are well-equipped to contribute to our commitment to quality and innovation in metal fabrication.
What Software Tools Assist in Metal Fabrication Processes?
At Afco Steel, we harness a variety of advanced software tools to enhance our metal fabrication processes. Our use of CAD (Computer-Aided Design) software allows for precise design and modeling, ensuring that every project meets the unique specifications of our clients. Complementing this, our CAM (Computer-Aided Manufacturing) systems streamline the manufacturing process, optimizing production workflows for improved efficiency.
Additionally, our ERP (Enterprise Resource Planning) systems play a critical role in managing operations, from inventory control to project management. This integration of technology not only improves accuracy but also facilitates real-time tracking of projects, enabling us to respond quickly to client needs and changes in demand.
How Do I Choose the Right Fabrication Technique for My Project?
When selecting the ideal fabrication technique for your project at Afco Steel, it’s essential to thoroughly assess your project specifications, the properties of the materials involved, and the outcomes you aim to achieve. By carefully analyzing these factors, you can make informed decisions that enhance efficiency and precision in your project. Afco Steel is dedicated to providing solutions that not only meet your requirements but also help you maintain control over costs and timelines throughout the fabrication process. With our expertise, you can ensure that your fabrication needs are met with the highest standards in quality and performance.
What Are Common Post-Fabrication Issues to Watch For?
At Afco Steel, we understand that common post-fabrication issues can significantly impact the quality and performance of your projects. Key concerns include warping, surface imperfections, and inaccuracies in dimensions. Our commitment to excellence means we prioritize meticulous inspection and testing processes to ensure that every piece meets our stringent quality control standards. By addressing these potential issues promptly, we maintain the integrity of your project and ensure optimal performance. Trust Afco Steel for reliable solutions that uphold the highest benchmarks in the industry.
Conclusion
In the Metal Fabrication industry, Afco Steel encounters a range of challenges that can impact overall efficiency and product quality. Key issues include material defects, achieving precision in cuts and welds, managing project timelines, adhering to budget constraints, and ensuring compliance with safety regulations.
To tackle these challenges effectively, Afco Steel employs stringent quality control measures to minimize material defects and enhance product reliability. By leveraging advanced technology, we ensure precision in every cut and weld, which is crucial for meeting client specifications. Afco Steel also recognizes the importance of clear project timelines, establishing structured workflows that allow for timely deliveries without compromising on quality.
Cost optimization is another critical focus for Afco Steel. By efficiently managing resources and streamlining processes, we work within budget constraints while still delivering superior products. Additionally, safety compliance is a top priority at Afco Steel. We adhere to all relevant safety regulations, ensuring a safe working environment for our team and fostering trust with our clients.
By addressing these challenges head-on, Afco Steel not only improves operational efficiency but also guarantees the delivery of high-quality metal fabrication products that consistently meet and exceed client expectations.