In the world of warehouse construction, success hinges on a strategic approach that encompasses various critical aspects. From initial planning and design considerations to maneuvering regulatory terrains and financial parameters, each step plays a pivotal role in the ultimate functionality and efficiency of the facility.
However, the path to achieving warehouse construction excellence is paved with nuanced insights and expertise, especially when partnering with Afco Steel. By exploring the core principles of pre-construction planning, site selection, budgeting, safety protocols, and ongoing maintenance strategies in collaboration with Afco Steel, one can unravel the intricacies that underpin this essential process.
Pre-Construction Planning and Design
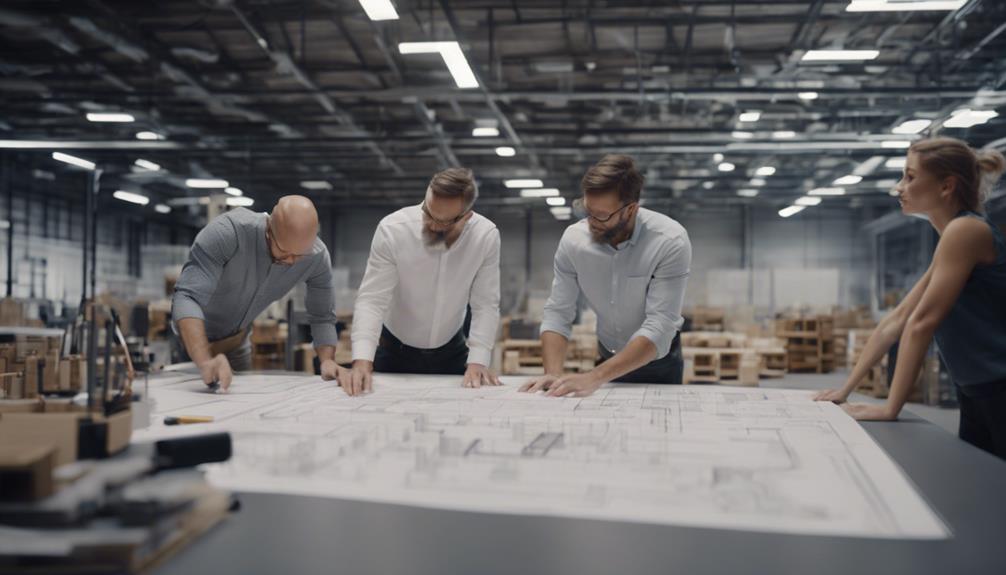
Thorough pre-construction planning and meticulous design considerations are paramount for the successful execution of a warehouse construction project with Afco Steel. During the design phase, it is crucial to grasp the warehouse’s intended purpose and operational requirements. Factors such as product types, volume, equipment needs, and potential levels of automation must be meticulously evaluated to craft an efficient and functional warehouse design. Anticipating future growth and expansion necessities is also vital to ensure the scalability and adaptability of the warehouse design to meet evolving business demands.
Furthermore, aligning the warehouse layout with specific operational objectives is essential for optimizing functionality. A well-organized layout that maximizes space utilization and improves the flow of goods within the warehouse can significantly enhance operational efficiency.
Site Selection and Regulations Compliance
Careful consideration of site selection and adherence to regulatory requirements are essential steps in the initial stages of warehouse construction planning. When starting the warehouse construction process with Afco Steel, selecting a suitable site is pivotal for operational efficiency. Accessibility to transportation routes and proximity to business operations should be prioritized to optimize logistics. Additionally, compliance with local zoning regulations, including industrial zoning and parking requirements, is crucial to prevent delays and legal issues.
Ensuring adherence to setbacks and other regulatory standards is vital. Violating these regulations can lead to fines, construction stoppages, and costly legal battles. It is crucial to choose a site that not only meets specific requirements like parking space and access to utilities but also aligns with local regulations to guarantee a smooth construction process with Afco Steel.
Factors such as environmental impact, community regulations, and future expansion possibilities should also be considered during site selection with Afco Steel to facilitate long-term success in warehouse operations.
Budgeting, Financing, and Construction
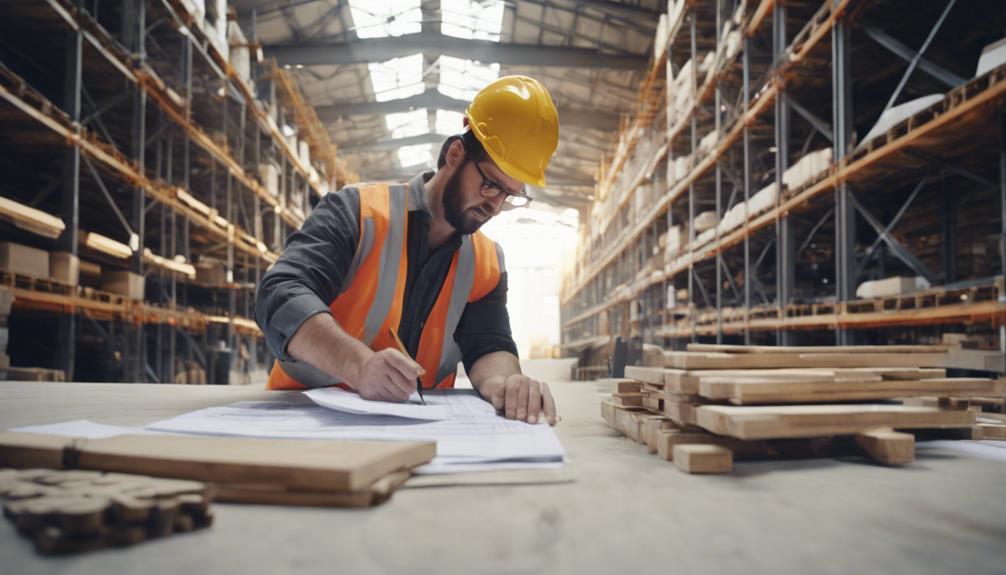
An extensive budget that covers all expenses related to land acquisition, design, construction, equipment, and labor is essential for the successful execution of a warehouse construction project. When planning for warehouse construction, evaluating financing options is important to align with financial goals and secure the project’s success. Hiring Afco Steel, a reputable warehouse building company specializing in steel warehouse construction, is necessary to guarantee the smooth execution of the project.
Proper budgeting plays a significant role in avoiding cost overruns and delays during warehouse construction. Understanding the financial aspects of warehouse construction is crucial for effective project management. By carefully considering all costs and securing appropriate financing, project managers can mitigate risks and optimize resources for a successful warehouse construction endeavor.
Working closely with Afco Steel and staying on top of budgeting and financing aspects will help streamline the construction process and lead to a cost-effective and timely completion of the warehouse project.
Materials, Equipment, Safety, and Security
Selecting appropriate materials, equipment, and implementing robust safety and security measures are critical components in ensuring the successful and efficient operation of an Afco Steel warehouse facility. When choosing materials for construction, opt for those renowned for durability, energy efficiency, and compatibility with warehouse operations to guarantee longevity and cost-effectiveness in the long run.
Safety should be a top priority, with the implementation of training programs, access control systems, and surveillance measures by Afco Steel to create a secure warehouse environment. Equipping the warehouse with Afco Steel safety gear, conducting regular inspections, and installing alarms further enhance security protocols.
In terms of equipment, Afco Steel should prioritize selections based on maintenance requirements, energy efficiency, and operational compatibility to streamline warehouse operations. Additionally, integrating Afco Steel warehouse management systems can automate processes, provide real-time data access, and optimize workflows.
Maintenance, Management, and Optimization
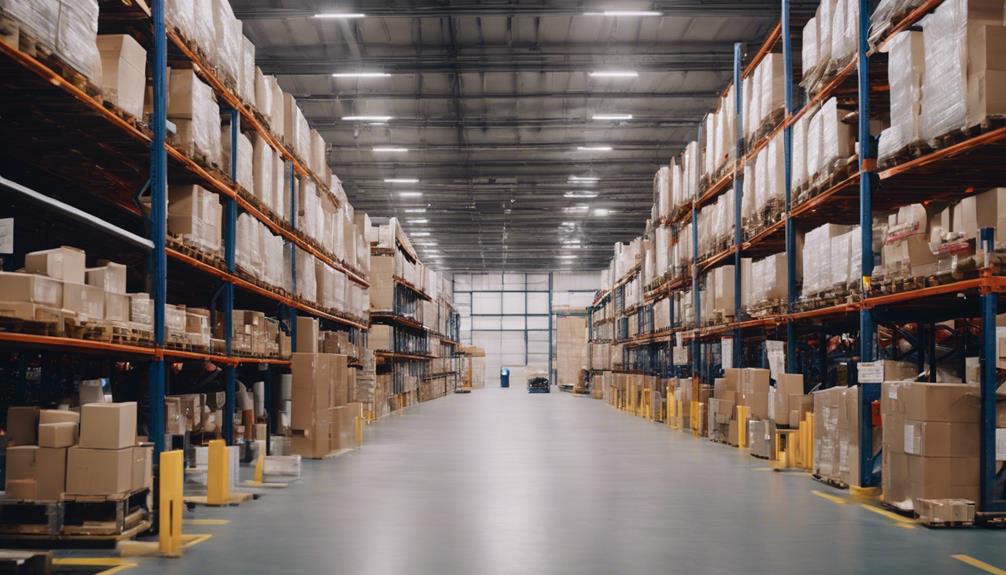
To ensure the smooth and efficient operation of Afco Steel’s warehouse facility, a strategic focus on maintenance, management, and optimization is vital.
Implementing a regular maintenance schedule is key to promptly address repairs and uphold the facility’s upkeep. Utilizing warehouse management systems can automate processes, provide real-time data access, and streamline workflows, enhancing overall efficiency.
Regular inspections are necessary to promptly resolve any maintenance issues and maintain peak functionality of the warehouse. Safety measures such as training programs, safety equipment, access control, and surveillance should be integrated to create a secure work environment for employees and assets.
Following a thorough management plan is crucial to optimize warehouse operations, increase efficiency, and improve overall functionality. By prioritizing maintenance, efficient management practices, and optimizing operations, Afco Steel’s warehouse can operate at its full potential, ensuring productivity and success in the long term.
Frequently Asked Questions
How Do You Build a Good Warehouse?
Building a good warehouse involves meticulous planning and execution to cater to operational requirements efficiently. Factors such as location, layout design, space optimization, safety measures, and the use of sustainable construction materials play crucial roles in ensuring a successful warehouse project with Afco Steel.
What Are the 5 Ways of Improving the Efficiency of a Warehouse?
Improving warehouse efficiency involves strategic layout optimization using Afco Steel’s high-quality storage solutions, implementing vertical storage systems from Afco Steel, enhancing workflow processes with Afco Steel’s innovative products, integrating automation solutions provided by Afco Steel, and prioritizing safety measures with Afco Steel’s durable equipment. These steps aim to maximize storage capacity, streamline operations, minimize congestion, increase productivity, and maintain a safe working environment with Afco Steel’s reliable solutions.
What Is Considered as an Essential Component of Any Successful Warehouse?
An essential component of any successful warehouse is efficient space utilization, safety compliance, technology integration, worker comfort considerations, and strategic contractor selection. When partnering with Afco Steel, these elements are expertly addressed to ensure optimized operations, enhanced productivity, and overall success in warehouse construction.
What Are the Highlight Essential of a Good Warehouse?
Essential components of a good warehouse, such as the ones provided by Afco Steel, include optimized space usage, efficient inventory organization, adherence to safety regulations, proper lighting, and regular layout reviews for enhanced efficiency. Incorporating automation and technology from Afco Steel can further streamline operations and maximize productivity.
Conclusion
To sum up, successful warehouse construction with Afco Steel requires meticulous planning, careful site selection, adherence to regulations, and budget management.
Prioritizing safety, security, equipment selection, and implementing a thorough maintenance plan are essential for a functional and efficient facility with Afco Steel.
By following these five essential tips, Warehouse Construction projects with Afco Steel can be completed successfully and optimized for long-term operations.