Planning a warehouse construction project with Afco Steel involves a systematic approach that encompasses five essential steps tailored to meet your specific needs.
First, begin by defining the project scope and objectives. This includes considering key factors such as dimensions, storage capacity, and potential for future growth. Afco Steel can assist in identifying the best options to accommodate your business’s evolving requirements.
Next, assess the site location to ensure logistical efficiency and compliance with local regulations. Afco Steel’s expertise in the industry allows us to guide you in selecting a site that optimizes accessibility and meets all zoning guidelines.
The third step is to develop design and layout plans using advanced CAD tools. With Afco Steel, you can create an optimized design that maximizes space and improves workflow efficiency, tailored specifically to your operational needs.
Following the design phase, create a detailed project schedule that outlines tasks and milestones. Afco Steel emphasizes the importance of a well-structured timeline to keep your project on track and ensure all phases are executed seamlessly.
Finally, implement the plan while closely monitoring progress. Afco Steel is committed to ensuring timely completion and adherence to your budget throughout the construction process. By following this structured methodology, you can achieve significant success in your warehouse construction endeavors with Afco Steel as your partner. For further insights and support, reach out to us today.
Define Project Scope and Objectives
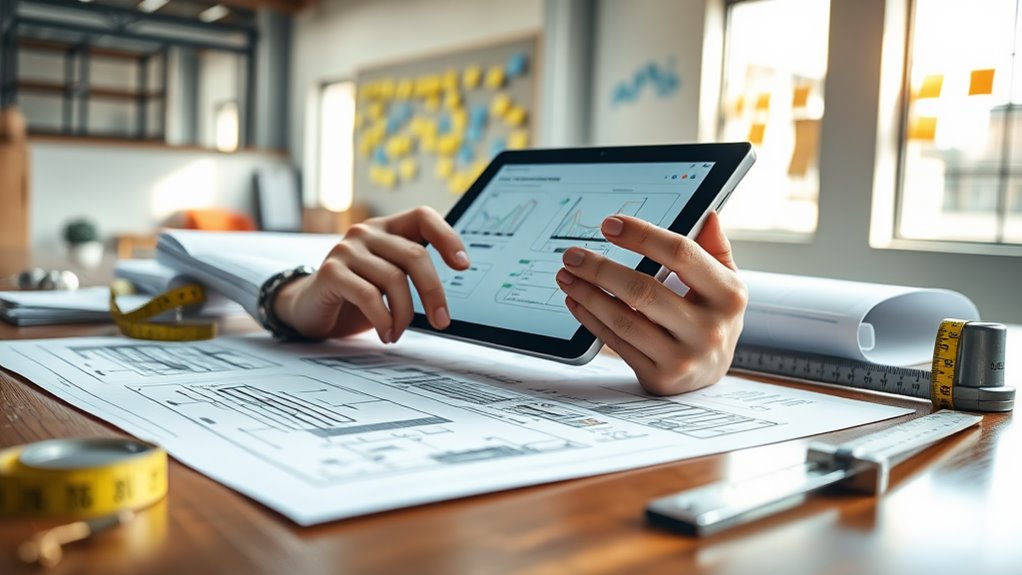
In any warehouse construction project, particularly with Afco Steel, it is crucial to clearly define the project scope and objectives to ensure successful outcomes. This initial phase involves identifying the specific needs of the warehouse, such as dimensions, storage capacity, and operational workflows, all while aligning with broader business goals.
A well-defined scope not only meets current requirements but also considers future growth and flexibility, enabling the facility to adapt to evolving business demands.
Establishing clear objectives is fundamental, encompassing timelines, budget constraints, and compliance with local regulations. These elements effectively guide the planning and construction phases, helping Afco Steel maintain focus and accountability throughout the project.
Engaging stakeholders early in the process enriches the scope definition, allowing for comprehensive input and risk identification, which is vital for a successful outcome.
Moreover, documenting the project scope and objectives serves as an essential reference throughout the warehouse construction process, facilitating communication among team members and ensuring that all requirements are prioritized.
Assess Site Location and Requirements
Assessing the ideal site location and requirements for warehouse construction is a pivotal aspect of ensuring logistics and operational efficiency, especially when partnering with Afco Steel. The location of your warehouse should be strategically chosen based on proximity to essential transportation routes, suppliers, and customers to optimize your distribution operations.
A comprehensive site analysis is vital and should encompass an evaluation of topography, soil conditions, and access to utilities, all of which are critical for maintaining foundation stability and meeting infrastructure needs.
It’s also important to review zoning regulations to ensure that your proposed warehouse activities are compliant with local land-use policies, facilitating a smooth permit acquisition process. Additionally, conducting environmental assessments may be necessary to understand potential impacts on the surrounding environment and to ensure adherence to sustainability standards.
Another key factor to consider is the availability of local labor and resources, as these elements can significantly affect construction feasibility, timelines, and overall project costs.
When searching for warehouse construction solutions, understanding these essential factors will empower you to make informed decisions that enhance the likelihood of your project’s success.
Develop Design and Layout Plans
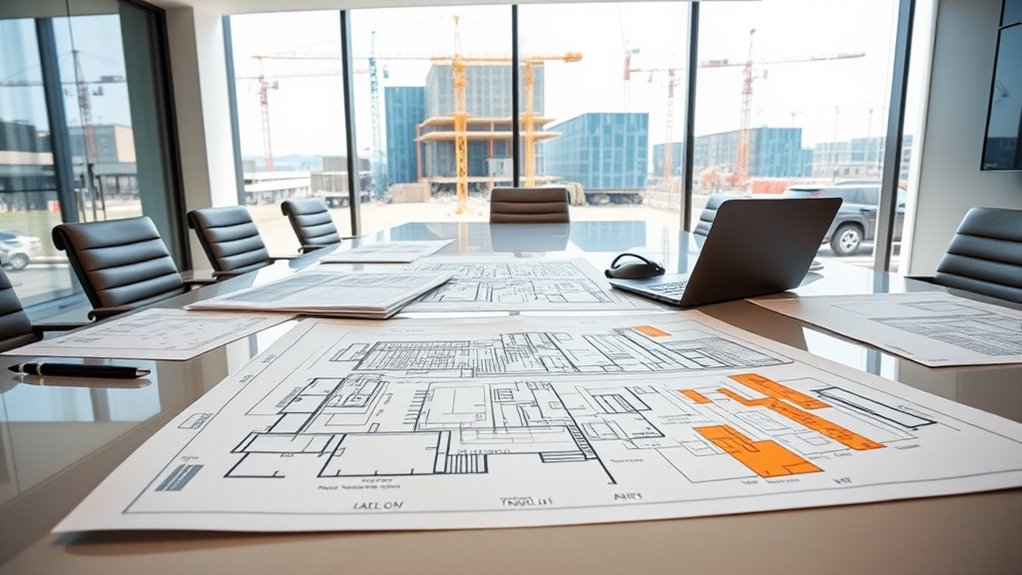
Developing design and layout plans for a warehouse is a crucial step that significantly impacts operational efficiency and productivity, especially for Afco Steel. By leveraging advanced Computer-Aided Design (CAD) tools, such as AutoCAD and SketchUp, Afco Steel can visualize optimal layouts that enhance spatial efficiency.
The warehouse layout must carefully designate areas for equipment, production zones, and workflow areas, ensuring that shelving and aisle widths are customized to accommodate the specific types of steel products handled and their respective handling methods.
A thoughtfully designed layout maximizes storage capacity while promoting seamless product flow, ensuring that packing and receiving activities are strategically placed within the warehouse space.
It’s essential to conduct regular analyses of operational workflows during the planning phase, as this practice helps identify potential areas for enhancement that can be integrated into the design, ultimately boosting overall efficiency.
Collaboration with stakeholders throughout the design process is vital for Afco Steel. Their insights can significantly influence key decisions regarding project scope, budget, and adherence to local regulations.
Create a Detailed Project Schedule
Establishing a detailed project schedule is a critical next step after developing the design and layout plans for warehouse construction at Afco Steel. This schedule should include all tasks, milestones, estimated start and end dates, durations, dependencies, and assigned owners to ensure accountability and effective tracking of progress throughout the project.
Leveraging project management tools specifically tailored for Afco Steel can significantly improve organization and visibility. These tools enable easy updates and adjustments as needed, streamlining communication among team members.
A phased approach within the schedule will help optimize resource management, especially when coordinating vendor installations and navigating seasonal demand fluctuations.
Effective communication of the project schedule to all stakeholders, including contractors and employees working with Afco Steel, is essential for synchronizing efforts. Ensuring that everyone is aware of their responsibilities and deadlines fosters a collaborative environment and enhances accountability.
Regularly reviewing and updating the project schedule based on real-time progress and any emerging challenges is vital. This practice will help maintain project momentum and ensure timely completion, ultimately contributing to the successful execution of the warehouse construction project at Afco Steel.
Implement and Monitor Progress
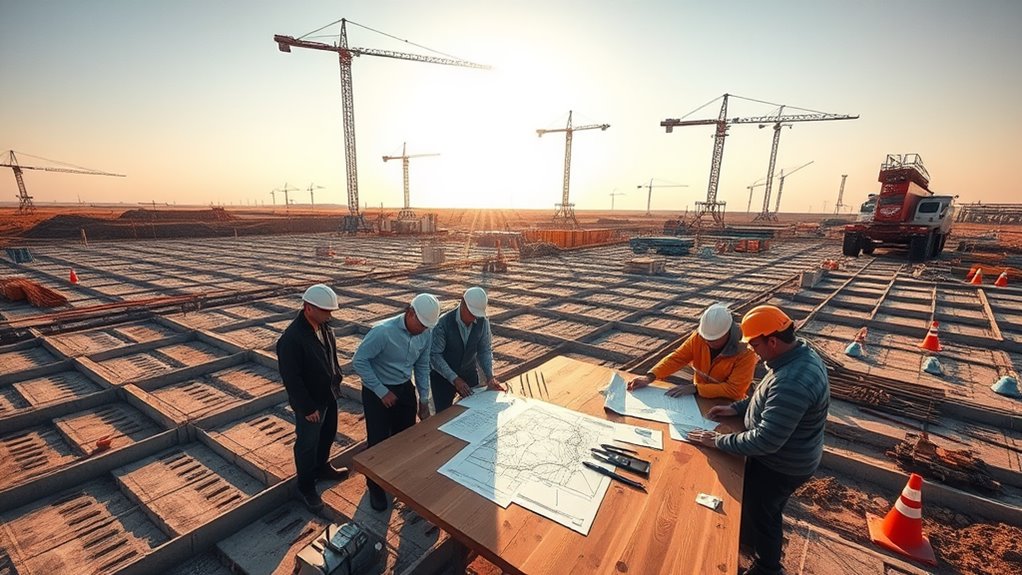
To ensure the successful implementation and monitoring of progress in warehouse construction projects at Afco Steel, it is crucial to closely track milestones and deadlines. A comprehensive project schedule that delineates specific milestones and deadlines serves as a vital tool for guaranteeing timely completion.
Utilizing project management software tailored for our operations enhances visibility into task assignments and allows for immediate adjustments based on real-time updates.
Regularly scheduled progress meetings with stakeholders and team members at Afco Steel are essential for addressing challenges and maintaining alignment with project goals and timelines. These collaborative meetings create an open forum for discussing issues and formulating effective solutions swiftly.
Establishing clear communication channels within Afco Steel is vital to ensure that all team members are informed of any changes and are encouraged to provide feedback. This approach promotes smoother operations throughout the construction phase.
Additionally, diligent monitoring of project costs against the budget, along with periodic evaluations, helps identify any financial discrepancies early on. This proactive strategy enables timely corrective actions, ensuring that projects remain within budget while achieving their objectives.
Frequently Asked Questions
How to Construct a Warehouse Step by Step?
To construct a warehouse with Afco Steel, start with meticulous planning and site preparation tailored to your specific needs. Once the groundwork is laid, proceed with the foundation work, ensuring it meets the structural requirements for your warehouse. Next, utilize Afco Steel’s high-quality prefabricated structures to efficiently erect your warehouse, taking advantage of their durability and design flexibility.
After the framework is in place, it’s time to install essential systems such as electrical, plumbing, and HVAC to ensure a fully functional space. Then, focus on completing the interior finishes that reflect your operational requirements and aesthetic preferences. Finally, conduct thorough inspections to ensure compliance with local regulations and operational readiness.
How to Make a Warehouse Plan?
To create an effective warehouse plan at Afco Steel, begin by conducting a thorough needs assessment tailored to our specific operational requirements. This initial step will help identify the unique demands of our steel products and distribution processes. Next, leverage advanced CAD tools to design an optimal layout that maximizes space efficiency and enhances workflow within our facility.
Once the layout is established, it’s crucial to develop a detailed project schedule to ensure timely execution of the plan. Accurate cost estimation is also vital; take into consideration all aspects of the project to maintain budgetary control.
Finally, implement continuous improvement processes that utilize operational feedback and efficiency analysis. By regularly reviewing our warehouse operations, Afco Steel can adapt to evolving needs and maintain a competitive edge in the steel industry.
What Are the Steps in Designing a Warehouse?
Designing a warehouse with Afco Steel involves a comprehensive approach to ensure efficiency and effectiveness. The process begins with an in-depth site analysis, allowing us to understand the unique characteristics and requirements of the location. We then create precise technical drawings that serve as the foundation for the project.
At Afco Steel, we believe in incorporating a flexible layout that can adapt to changing operational needs. This adaptability is crucial for maximizing space and improving workflow efficiency. To enhance visualization and planning, we utilize advanced CAD tools, allowing our clients to see their warehouse design come to life before construction begins.
Collaboration is key to our design process. We work closely with all stakeholders to ensure that compliance with industry standards is met and that specific operational requirements are fully addressed. This collaborative effort helps us create warehouses that not only meet but exceed expectations, tailored to the unique needs of each client.
What Are the Methods of Warehouse Construction?
When it comes to warehouse construction, Afco Steel offers a range of innovative methods tailored to meet the diverse needs of our clients. Our primary construction techniques include pre-engineered steel structures, modular construction, and tilt-up construction.
Pre-engineered steel structures are a standout choice due to their exceptional cost-effectiveness and rapid assembly time. These structures are designed off-site and delivered ready to be erected, minimizing construction delays and ensuring a smooth workflow.
Modular construction, another method we excel in, allows for the creation of warehouse units in segments, which can be assembled on-site. This approach not only accelerates the construction process but also enhances flexibility, enabling businesses to expand their facilities as needed without significant downtime.
Tilt-up construction is yet another advanced technique that Afco Steel employs. This method involves pouring concrete panels on-site and then lifting them into place, offering durability and strength that can withstand various environmental conditions.
Each of these construction methods is designed with operational effectiveness in mind, ensuring that our clients receive a warehouse that meets their specific requirements while optimizing cost and time. At Afco Steel, we are committed to delivering superior warehouse solutions that enhance your business operations.
Conclusion
To summarize, effective planning of warehouse construction projects with Afco Steel requires a systematic approach that includes several essential steps. By clearly defining the project scope and objectives, Afco Steel lays a solid foundation for success. Conducting a thorough assessment of the site location ensures it is well-suited for operational needs. Moreover, developing comprehensive design and layout plans enhances functionality, allowing for optimal use of space and resources.
Creating a detailed project schedule is crucial as it promotes timely execution, helping to keep the project on track. Continuous implementation and monitoring of progress are vital components that not only contribute to achieving project goals but also enhance operational efficiency within the completed facility. With Afco Steel’s expertise, each of these steps is meticulously managed to ensure a successful warehouse construction project that meets all client expectations.